Health and safety at work have been the major themes of recent decades. Between the COVID-19 pandemic, evolving regulations, and increased social awareness, maintaining high workplace well-being has become a necessity. But how can you know what’s happening on the ground? How can you prevent workplace accidents? How can you ensure healthy working conditions for your employees? The solution: the safety briefing. This daily or weekly meeting allows you to easily initiate a health and safety approach in your organization. MoveWORK offers all its tips for setting up and optimizing the performance of your safety briefings.
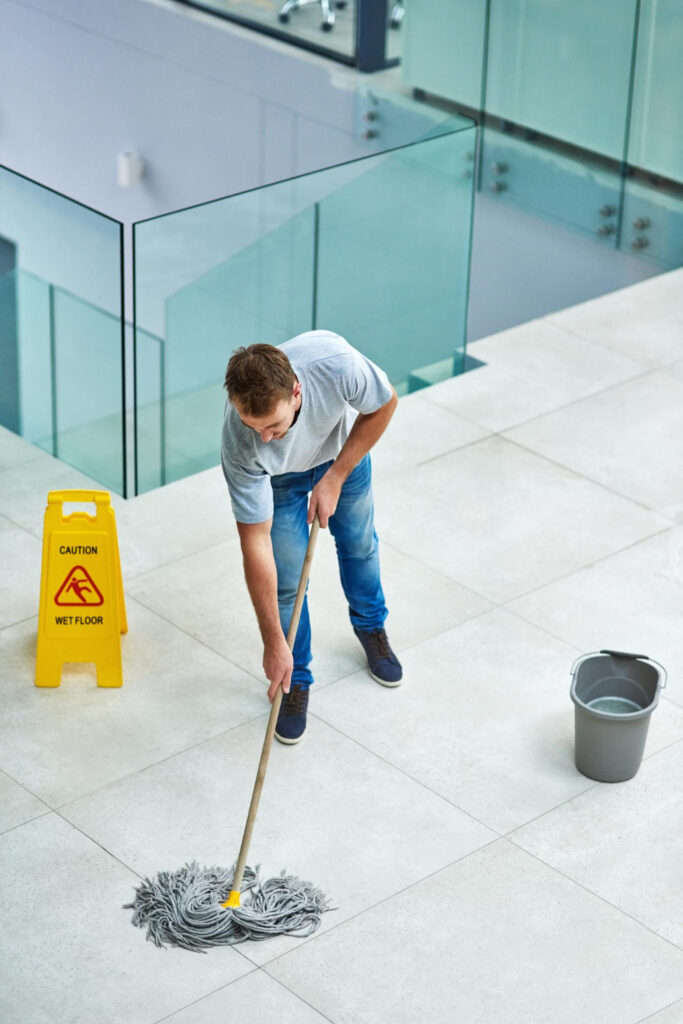
Why implement a safety briefing?
Regardless of the industry or type of company, communication is key to smooth operations. That’s why regular discussions with your teams are inherently beneficial. In this context, a safety briefing is a short meeting held at regular intervals in the workplace to discuss health and safety issues, as the name suggests.
The main goal is to raise employee awareness about the risks associated with their operational tasks and to identify hazardous situations on-site or at client job sites. The safety briefing also serves to remind employees of best practices and promote a culture of accident prevention. These debriefings are usually conducted by a QSE manager, a supervisor, or the team leader.
The benefits of safety briefings are numerous:
- Educating employees and reinforcing safe behaviors
- Reducing the number of workplace accidents and incidents
- Improving inter- and intra-team coordination
- Immediate resolution of hazardous situations
- Maintaining a safe work environment and enhancing working conditions
- Ensuring regulatory compliance
- Lowering costs related to workplace accidents, occupational diseases, legal disputes, and downtime
Investors, consumers, and other stakeholders are increasingly emphasizing corporate social responsibility. Companies are thus encouraged to improve their practices to maintain their reputation and attractiveness. Safety briefings are the best way for employers to ensure safe and supportive work environments.
Organizing a safety briefing effectively
To optimize the effectiveness of your safety briefing, the first step is preparation. Indeed, leading a briefing is not as simple as it may seem: you need to capture your employees’ attention and subtly engage them in the discussion. Your field agents are a goldmine of information, but sometimes it is challenging to articulate what is experienced or observed daily.
To achieve this, you must first choose a relevant topic that addresses your team’s safety concerns. Rely on current events: has a new protocol been implemented? Have recent incidents been reported? Is the same type of anomaly being detected repeatedly? A well-chosen topic resonates with participants and ensures their engagement.
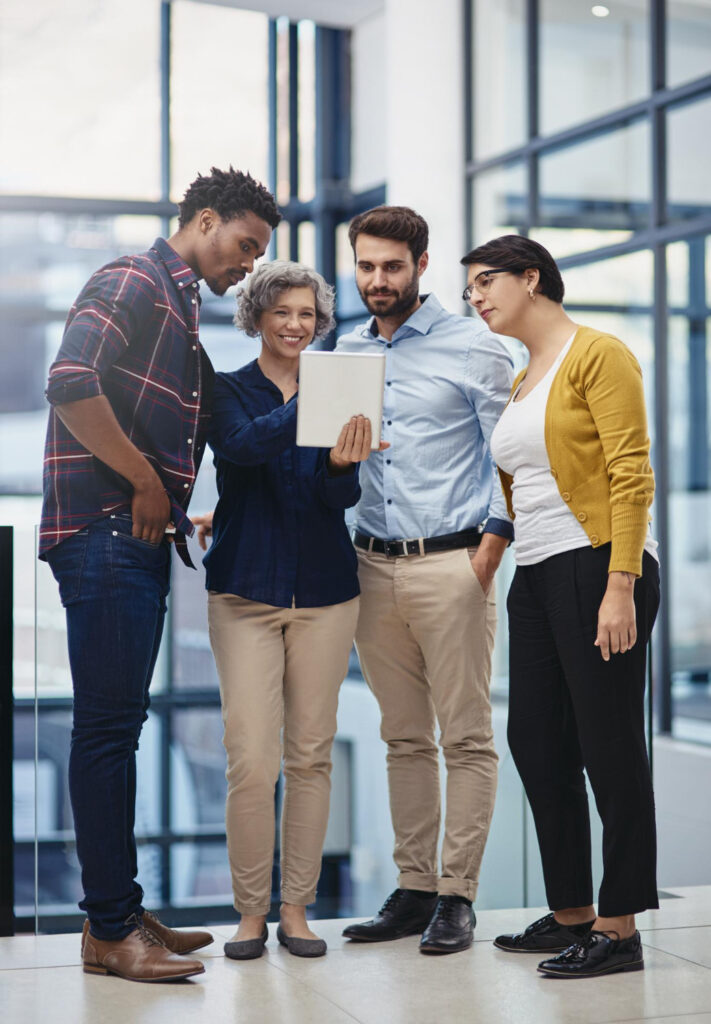
Next, you need to set clear objectives and communicate the purpose of the safety briefing to your agents. These indicators will provide a precise direction for the discussion, a logical sequence of topics to cover, and define an appropriate duration for each point. Using visual aids, concrete reporting, and testimonials can greatly enhance the safety briefing. With quantified data, your points are better illustrated, participants’ attention is captured, and discussions become more constructive.
Track the movements of your operation in real time
As mentioned earlier, the safety briefing should be based on concrete and measurable field feedback. However, the constantly changing daily activities of the staff can lead to certain points being forgotten, misidentified, or sometimes distorted. To optimize the effectiveness of these meetings, the manager must implement tools to collect and centralize data in real time. Technological advancements have enabled the development of equipment that facilitates the monitoring of working conditions and the identification of risks.
Connected equipment: Allies of safety briefings
To collect data, what could be better than new technologies? The safety manager has a wide range of equipment to identify risk situations on the ground. Connected equipment collects real-time field information and then instantly feeds it into your management tool. These indicators will then support the safety briefings and facilitate discussion.
Several types of connected equipment can be useful for your safety briefing:
- Pointing Devices : In cases of absence or tardiness, the anomaly is immediately reported to the manager or team leader. If it occurs repeatedly, the issue can be addressed in the safety briefing to identify the cause of the problem, such as difficult access.
- Connected Hygiene Equipment : These devices measure the levels of sanitary equipment such as soap dispensers, paper towel dispensers, or trash cans. With this tracking, the manager can measure service interruptions or the consumption of supplies. Depending on the situation, the safety briefing is an excellent opportunity to understand issues like excessive consumption of supplies or recurring shortages in specific areas.
- Connected Stations : Usually equipped with service kiosks, these tools are an excellent way to report intervention requests and incidents detected on-site. With immediate data transfer to the sector manager, situations can be quickly addressed. These elements also provide a wealth of information to feed into daily or weekly safety briefings.
IoT sensors: Ensuring a healthy environment
IoT sensors are another effective tool for measuring flows in your operation. By tracking environmental indicators, they measure the cleanliness of the work environment and detect intervention needs. Among these sensors, you’ll find:
- Environmental Sensors : These devices measure temperature, humidity, air quality, and a range of other parameters to detect abnormal conditions. They can automatically trigger interventions, such as ventilation or air conditioning activation. If anomalies recur, these data points can be analyzed during safety briefings.
- Occupancy Sensors : These tools measure the flow of people present or having been present in a specific location. This allows the manager to identify if certain areas are more occupied than others and whether the services provided in these locations are sufficient. These issues can be addressed and discussed with staff on-site during safety briefings.
Vibration Sensors : These devices monitor machines and equipment to detect abnormal vibrations that may indicate potential malfunctions. They help assess tool wear and ensure a continuously safe working environment.
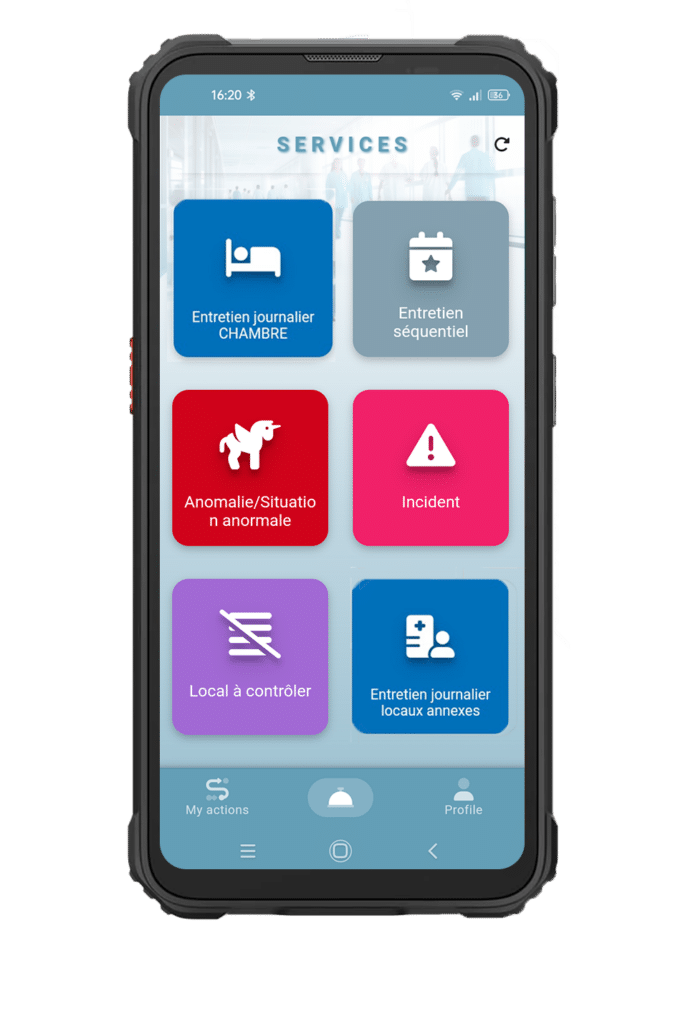
Mobile applications : The essential tool for enhancing safety briefings
Mobile apps are ideal tools for enhancing safety briefings in the workplace. They allow for the rapid centralization and dissemination of critical information while facilitating collaboration among staff. With these apps, employees can instantly report incidents or hazards encountered on-site. They can locate the anomaly, describe it, and trigger the necessary corrective actions.
Additionally, mobile apps provide a useful history of actions during safety briefings. It is easy to trace the origin of a hazardous situation or find the actions that triggered it. These tools also provide access to real-time updates on safety protocols.
Analyze occupational health and safety data
Collecting data is a good thing, but where should it be centralized? How do you correlate the information? How do you analyze it and then present it during your safety briefing? This is where management and operational control systems come into play!
These intelligent software platforms or systems allow you to consolidate all your operational data into a single interface. Beyond simple data recording, they link information based on coherence and origin. Anomaly detection algorithms analyze data in real-time to identify abnormal behaviors or conditions. With machine learning, predictive systems help manage potential failures before they occur.
To present reports during safety briefings, managers have access to dynamic dashboards. These dashboards provide an overview of operational conditions and enable quick and effective analysis of collected data in graphical form.
By combining these technological tools, operations can enhance their ability to detect and respond rapidly to undesirable situations, thereby increasing safety, efficiency, and productivity.
MoveWORK Flow: The solution to enhance the effectiveness of safety briefings
Thanks to its expertise in Facility Management, MoveWORK has developed simple and intuitive tools to streamline your QHSE processes. With a solution comprising the MoveWORK Flow management platform, mobile applications, and a connected equipment ecosystem, the reporting of anomalies or incidents on-site in real time is fully digitized. All this data feeds into your safety briefings, making for more enriching discussions.
With MoveWORK solutions, incident reporting is multi-channel:
- Via the myMissions Indoor app : With this mobile application, cleaning staff can report a hazardous situation or incident on-site with just one click. The information is instantly uploaded and centralized in the MoveWORK Flow platform and in the manager’s app, myDecisions.
- Via the myDecisions app : Through myDecisions, supervisors can perform quality checks. If a non-compliance is detected, the anomaly is automatically reported in the MoveWORK platform.
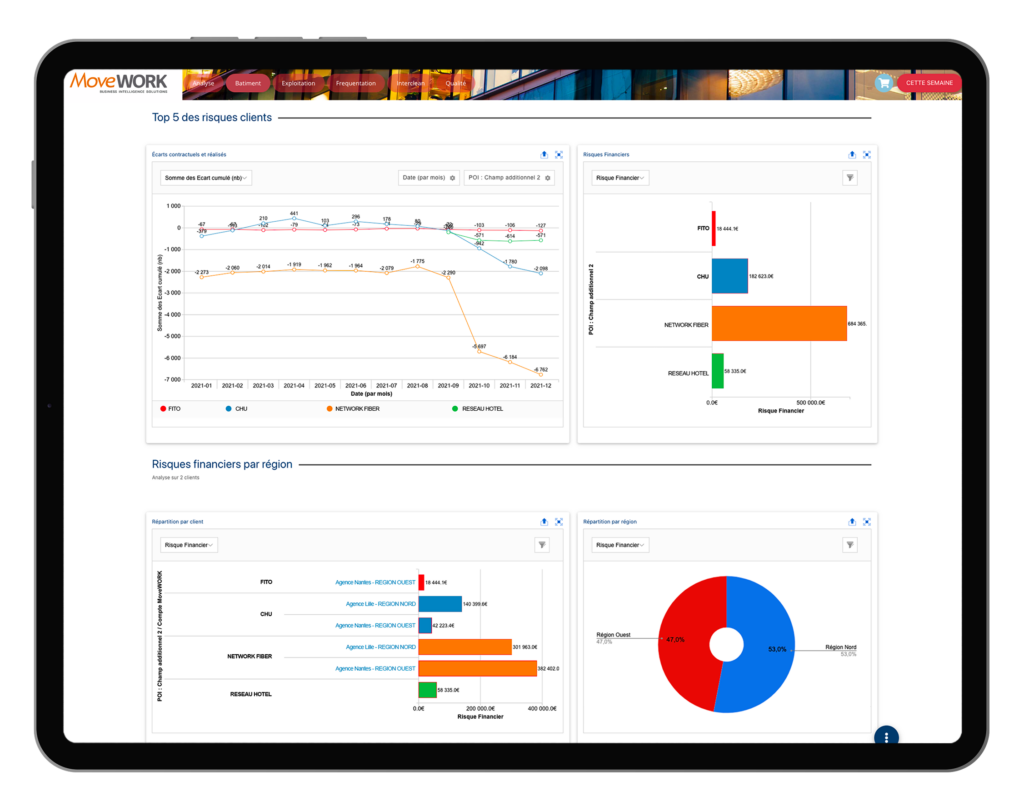
Via connected kiosks : MoveWORK offers connected kiosks with service stations that allow occupants to make instant requests or reports.
Via the MoveWORK Flow platform : The platform enables the creation of customized workspaces, including service kiosks for incident reporting or intervention requests. These workspaces can be restricted to specific user types (e.g., frontline managers, service heads, contractors) and have personalized access controls.
- Via pre-installed equipment : The MoveWORK Flow platform enables the generation of service kiosks that are easily accessible via a simple URL link. These service kiosks can be easily integrated into existing tools such as reception kiosks, tablets, websites, intranets, or fixed workstations.
Once reports are collected, issues are automatically processed within our MoveWORK Flow platform. The platform provides clear and transparent dashboards on detected anomalies and facilitates easy discussion of these issues during safety briefings. Additionally, MoveWORK Flow’s intelligent algorithm smartly triggers appropriate corrective actions based on the reported situation. Everything is centralized into customized reports to ensure precise traceability of events and quality indicators. With a unified view of operational incidents, your safety briefings are continuously updated. MoveWORK solutions thus provide you with all the tools needed to enhance your team’s daily operations and ensure a secure working environment at all times.